Трансмісія
Зчеплення
Насамперед необхідно вибрати та обґрунтувати конструкцію зчеплення. Вибираємо за прототипом однодискове механічне зчеплення.
Змн. |
Арк. |
№ докум. |
Підпис |
Дата |
Арк. |
КП.А.АТ-091.19.ПЗ.ЧДТУ |
Розроá. |
Савенчук В.В. |
Перевір. |
Хоменко І. М. |
Реценз. |
Н. Контр. |
Хоменко І. М. |
Затверд. |
3 Трансмісія |
Літ. |
Аркушів |
АТ-091 |
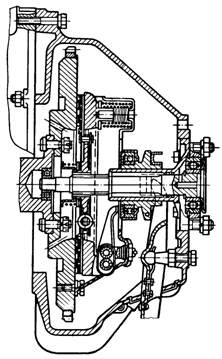
Рисунок 3.1 – Рисунок однодискового механічного зчеплення
Далі обчислюємо середній радіус тертя Rср, м:
(3.1)
де в = 1,75...2,5 – коефіцієнт запасу зчеплення;
Мк max =206,41 Н∙м – максимальне значення крутого моменту двигуна;
p0 = 0,15...0,30 МПа – тиск на фрикційну накладку;
м = 0,25...0,35 – коефіцієнт тертя фрикційних поверхонь;
z – кількість поверхонь тертя – z = 2;
К = b/Rср = 0,375...0,630 – коефіцієнт ширини фікційної накладки.
Із зростанням Мк max значення К збільшується; b = К∙Rср – ширина фриційної накладки.
Чисельне значення :
м.
Зовнішній діаметр фрикційної накладки становить:
Змн. |
Арк. |
№ докум. |
Підпис |
Дата |
Арк. |
КП.А.АТ-091.19.ПЗ.ЧДТУ |
м.
Обчислену величину D округляють згідно з існуючими правилами та порівнюють із значеннями, наведеними в ГОСТ 1786-95.
Якщо обчислене значення не збігається зі стандартом, то вибирають найближче більше і вважають його дійсним значенням діаметра накладки Dд =270мм. За стандартом визначаємо і внутрішній діаметр d=139мм.
Дійсне значення середнього радіуса тертя
(3.3)
Чисельне значення:
м.
Нормальна сила, яка діє на поверхні тертя,
кН. (3.4)
Чисельне значення:
кН.
У випадку, коли значення Рn більше за 9,..10 кН, то для полегшення керування зчепленням доцільно збільшити кількість поверхонь тертя або запроектувати підсилювач.
Якщо силовий елемент багатопружинний, то силу пружності кожної пружини знаходять із виразу
(3.5)
Чисельне значення:
Н,
де і – кількість пружин.
На міцність пружини розраховують, виходячи з розрахункового зусилля, яке виникає при додатковій деформації Δf пружини коли виключаємо зчеплення:
Н, (3.6)
де К – коефіцієнт, що враховує нерівномірність навантаження пружин через їх неоднакову довжину та жорсткість, К = І,І...І,2.
Діаметр дроту, із якого виготовляють пружину, мм,
(3.7)
Чисельне значення:
м
Діаметр дроту, із якого виготовляють пружину приймаємо 4 мм.
де Dср – середній діаметр пружини (вибирають із конструктивних міркувань);
– допустиме напруження кручення витків пружини,
= 800 МПа.
Робочу кількість витків пружини знаходи за формулою:
. (3.8)
Чисельне значення:
,
де = 3 мм для однодискового зчеплення;
= 4 мм для дводискового;
Змн. |
Арк. |
№ докум. |
Підпис |
Дата |
Арк. |
КП.А.АТ-091.19.ПЗ.ЧДТУ |
= Рпр.розр– Рпр – збільшення сили пружності при виключенні зчеплення, Н.
Н.
Повна кількість витків пружини:
nпр = n + (1,5...2,0)=2,3+2,0=4,3. (3.9)
Приймаємо nпр = 5.
Коробка передач (КП)
За результатами розрахунку передавальних чисел і вибору типу коробки передач (дво– або тривалова), визначають число зубців усіх шестерень (за винятком шестерень заднього ходу), знаходять відстань між осями валів, орієнтовні габаритні розміри коробки передач та креслять її кінематичну схему (рисунок 3.2).
Рисунок 3.2 – Кінематична схема КПП
Число зубців на кожній із передач визначають за передавальними числами, знайденими при тяговому розрахунку автомобіля.
Для забезпечення паралельності валів суми чисел зубців кожної пари шестерень повинні бути рівними. Якщо модуль і кут нахилу зубців у них однакові, то
z1+ z2 = z3 + z4 =... zib + zin. (3.10)
У тривалової коробки передач на всіх передачах, крім прямої, крутний момент передається через дві пари шестерень. Тому передавальне число i–ї передачі
, (3.11)
де z1, z2 – числа зубців шестерень приводу проміжного вала (z2 –на проміжному валі, z1 – на первинному);
zib, zin – числа зубців шестерень і–ї передачі (zib – на вторинному валі, zin – на проміжному).
Передавальне число зубчатої пари приводу проміжного вала коробки передач вибирають з інтервалу z2 / z1 = 1,8...2,5; а число зубців шестерні первинного вала z1 = 18. Тоді
(3.12)
Чисельне значення:
{ |
{ |
1передача
2 передача
3 передача
4 передача – пряма.
Змн. |
Арк. |
№ докум. |
Підпис |
Дата |
Арк. |
КП.А.АТ-091.19.ПЗ.ЧДТУ |
, мм, (3.13)
де Мрозр – розрахунковий крутний момент на валу шестерні, що розглядається (його значення визначають, виходячи з максимального крутного моменту двигуна, вибраного коефіцієнта запасу зчеплення та передавального числа від зчеплення до вала, який розглядають), в – кут нахилу зубців шестерень (на шестернях коробок передач легкових автомобілів в – 25...35°, вантажних і автобусів – в = 20...30о;
z – кількість зубців шестерні, що розглядається;
y – коефіцієнт форми зуба (для косозубих шестерень значення „ у ” вибирають із таблиці 6 (додаток 4), за приведеною кількістю зубців);
, (3.14)
b – ширина шестерні біля основи зуба (b = 20…25 мм для вантажних
автомобілів);
kу – допустиме напруження згину біля основи зуба з урахуванням ступеня його навантаження (табл. 7 додаток 4).
За обчисленим значенням модуля зубців, знаходимо розміри шестерень приводу проміжного вала та першої передачі, відстань між осями валів і орієнтовно габаритні розміри коробки передач (приймаючи, що ширина всіх шестерень однакова, а ширина вмикаючих пристроїв наближається до ширини двох шестерень).
(3.15)
Знаходимо модуля зубчастих коліс
Змн. |
Арк. |
№ докум. |
Підпис |
Дата |
Арк. |
КП.А.АТ-091.19.ПЗ.ЧДТУ |

Отримані значення модуля зубців округляємо до найбільшого за ГОСТ 9563–60 (СТ СЕВ 310–76, табл. 8 додаток 4).
Приймаємо значення m=10
Міцність зубців шестерень перевіряємо за контактними
напруженнями для першої пари шестерень:
, (3.16)
де в – кут нахилу зубців;
Р – колове зусилля, знайдене виходячи зі значень крутного моменту, що передається валом шестерні, Н;
Е – модуль поздовжньої пружності матеріалу (для сталі Е = 2,1 МПа);
– довжина лінії зачеплення;
r01, r02 – радіуси первинних кіл відповідних шестерень;
б = 30 ° – кут зачеплення шестерень.
Значення σст мають знаходитися в межах 1500...3000 МПа для прямозубих шестерень і 1000...2500 МПа – для косозубих.
Діаметри шестерень:
d1=m∙z=18∙10=180мм,
d2=m∙z=36∙10=360 мм.
Колова сила:
МПа
Умова за напруженнями виконується.
Карданна передача
Першим етапом у проектуванні карданної передачі, повинен бути вибір її схеми, кількості карданних валів та типу шарнірів, після чого необхідно накреслити її кінематичну схему (рисунок 3.3).
Змн. |
Арк. |
№ докум. |
Підпис |
Дата |
Арк. |
КП.А.АТ-091.19.ПЗ.ЧДТУ |
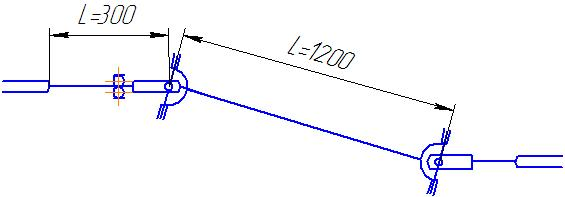
Рисунок 3.3 – Кінематична схема карданної передачі із проміжним валом
Для карданної передачі визначають внутрішній і зовнішній діаметри валів, виходячи з критичної частоти обертання ωкр,
ωкр = Кзап ωmax
де Кзап = І,2...2,0 – коефіцієнт запасу;
ωmax = (1,1...1,2)(ωдmax/ікmin)– максимально можлива при русі автомобіля частота обертання карданного вала;
ωдmax – частота обертання колінчастого вала двигуна при максимальному крутному моменті;
ωкmin – мінімально передавальне число коробки передач.
ωmax = (1,1...1,2)(ωдmax/ікmin)= 1,1(694.4/1)= 833.28 рад/с,(3.17)
ωкр = Кзап ωmax= 1,2∙ 833.28 = 916.6 рад/с(3.18)
Знаючи значення ωкр, с–1 та вибравши величину внутрішнього вала d= 78 мм, із ГОСТ 13758–89 знаходимо зовнішній діаметр D із виразу:
,
(3.19)
де D, d – відповідно зовнішній та внутрішній діаметри карданного вала;
Lb – довжина карданного вала (відстань між шарнірами),мм
Чисельне значення:
мм.
Наружний діаметр кардана приймаю D=92 мм
Змн. |
Арк. |
№ докум. |
Підпис |
Дата |
Арк. |
КП.А.АТ-091.19.ПЗ.ЧДТУ |
Обчислену величину D округляють до найближчої більшої, після чого перевіряють міцність вала на кручення за виразом:
(3.20)
Чисельне значення:
кПа
де Мрозр – розрахунковий крутний момент;
(3.21)
де в – коефіцієнт запасу зчеплення;
Мкmax – максимальний крутний момент двигуна;
іk1 – передавальне число першої передачі;
[ф] = 100 … 300 КПа.
Кут закручування вала, град,
(3.22)
Чисельне значення:
де G – модуль зсуву матеріалу (для сталі G = 80 ГПа);
Iр –полярний момент інерції перерізу для порожнистого вала:
(3.23)
Чисельне значення:
м4.
Кут закручування не повинен перевищувати 6о на кожний метр довжини. Якщо ц > 6 о , то доцільно збільшити площину перерізу карданного вала або зменшити його довжину.
Диференціал
Відповідно до призначення й типу автомобіля вибирають та обґрунтовують тип і конструкцію диференціала та креслять його кінематичну схему. Приймаємо конструкцію диференціала за прототипом (рисунок 3.4).
Рисунок 3.4 – Кінематична схема диференціала
Далі визначаємо максимальне значення коефіцієнта розподілу моменту між ведучими колесами автомобіля:
(3.36)
де і – внутрішнє передавальне число диференціала (для симетричних диференціалів і = І);
Кб – коефіцієнт блокування (Кб = 0,2...0,6 – для диференціалів із підвищеним тертям,).
Головна передача
Спочатку вибирають та обґрунтовують тип і конструктивні особливості головної передачі та креслять її кінематичну схему. Вибираємо кінематичну схему головної передачі за прототипом (рисунок 3.4).
Рисунок 3.4 – Кінематична схема головної передачі – подвійної
Змн. |
Арк. |
№ докум. |
Підпис |
Дата |
Арк. |
КП.А.АТ-091.19.ПЗ.ЧДТУ |
Якщо головна передача подвійна, то приймають передавальне число конічної пари:
(3.24)
Для пари циліндричних шестерень передавальне число знаходять із виразу
Змн. |
Арк. |
№ докум. |
Підпис |
Дата |
Арк. |
КП.А.АТ-091.19.ПЗ.ЧДТУ |
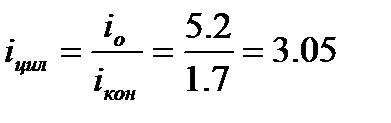
де і0 – передавальне число головної передачі, знайдене в тяговому розрахунку.
Задавшись значенням z3 =10, знаходять кількість зубців z4
(3.26)
Приймемо z4=30
Модуль зубців шестерень за більшим радіусом становить:
. (3.27)
Чисельне значення:
мм,
де Mрозр= Н– розрахунковий момент на ведучій шестерні;
в1 = 30...45° – кут нахилу спіралі зуба ведучої шестерні;
y – коефіцієнт форми зуба відповідно до приведеної кількості зубців. у = 0,136.
Приймемо m =8 мм
(3.28)
Чисельне значення:
де д – половина кута при вершині первинного конуса ведучої шестерні
Для пари конічних шестерень д становить:
(3.29)
Ζ1,Ζ2 – кількість зубців відповідно ведучої та веденої шестерень;
L = 90...150 мм – довжина твірної конуса;
– довжина зуба (найчастіше
);
у – напруження згину зуба (у = 420...550 МПа, менші значення при консольному кріпленні вала ведучої шестерні). Визначаємо за формулою:
. (3.30)
Чисельне значення: МПа,
де Р – умовне колове зусилля, що діє на середньому радіусі;
Н, (3.31)
Е– модуль поздовжньої пружності матеріалу (для сталі Е = 2,1 МПа);
– довжина лінії контакту
Змн. |
Арк. |
№ докум. |
Підпис |
Дата |
Арк. |
КП.А.АТ-091.19.ПЗ.ЧДТУ |
r1ср, r2ср – середні радіуси первинних конусів відповідно ведучої та веденої шестерень (у площині дії колової сили Р),
(3.32)
(3.33)
Чисельне значення:
мм
мм
r1осн, r2осн – радіуси основ первинних конусів відповідних шестерень; b1, b2 – ширина відповідних шестерень; б = 20° – кут зачеплення; rl1, rl2 – радіуси еквівалентних циліндричних шестерень, що відповідають ведучій і веденій шестерням),
(3.34)
(3.35)
Чисельне значення:
мм
мм
Привід ведучих коліс
Необхідно прийняти та обґрунтувати тип і конструкцію привода коліс, накреслити його кінематичну схему й описати особливості конструкції.
Рисунок 3.5 – Кінематична схема привода ведучих коліс
– згинаючий момент,
zк=4792∙2=9584Н – нормальна реакція полотна дороги, З (дорівнює силі ваги GK, що діє на колесо);
b= 0,21 – відстань від площини обертання колеса до небезпечного перерізу півосі, м;
Змн. |
Арк. |
№ докум. |
Підпис |
Дата |
Арк. |
КП.А.АТ-091.19.ПЗ.ЧДТУ |
– крутний момент, який передає піввісь;
rд =0.420 м – динамічний радіус колеса;
d – діаметр півосі, мм.
Діаметр півосі d визначають прийнявши напруження згину 100...140 МПа. За розрахунковий діаметр приймаємо більше значення з одержаних.
Прийнятий діаметр перевіряємо на закручування. Кут закручування півосі (град) визначаємо за формулою:
, (3.37)
де Мрозр – розрахункове значення крутного моменту, що передається піввіссю, Н∙м,
(3.38)
в =1,5 – коефіцієнт запасу зчеплення;
ік1, і0 – передавальні числа першої передачі коробки передач та головної передачі;
Км =1– коефіцієнт розподілу моменту за ведучими колесами;
l – довжина півосі (відстань від фланця до половини довжини шліців), м;
G – модуль зсуву матеріалу (для сталі G = 80 ГПа);
– полярний момент інерції, м4;
d – діаметр півосі, м.
Чисельне значення кута закручування:
Кут закручування не повинен перевищувати 9° на І м довжини.
Діаметр розвантаженої півосі визначають з умов її міцності при крученні:
(3.39)
Чисельне значення:
мм
де [ф] = 500...700 МПа – допустиме напруження кручення.
Змн. |
Арк. |
№ докум. |
Підпис |
Дата |
Арк. |
КП.А.АТ-091.19.ПЗ.ЧДТУ |
Розроá. |
Савенчук В. В, |
Перевір. |
Хоменко И. М. |
Реценз. |
Н. Контр. |
Хоменко И. М. |
Затверд. |
4. Ходова система |
Літ. |
Аркушів |
АТ-091 |
Підвіска
Послідовність розрахунку циліндричної пружини (передня підвіска).
Діаметр дроту пружини знаходять із виразу
, (4.1);
де Рпр – стискуюче зусилля, Н (Рпр = Zк);
[ф] = 1000 МПа – допустимі напруги кручення.
Dср – середній діаметр пружини, м (вибирають конструктивно).
м.
Тоді число робочих витків пружини становить:
, (4.2);
де f = fдин + fст,
G – модуль зсуву (для сталі G= 85 ГПа).
Повне число витків пружини nп = nр +(1,5...2,0).
.
Послідовність розрахунку ресори (задня підвіска).
Проектуючи, приймають співвідношення між динамічним і статичним навантаженням ресор Zдин = (2…3) Zcт для автомобілів, що експлуатуються в основному на дорогах із штучним покриттям;
Zдин = (3···4) Zcт – для автомобілів, які експлуатуються в основному на ґрунтових дорогах та в умовах бездоріжжя fдин = (0,7...0,9) fст – для вантажних автомобілів.
Статичний прогин визначають із виразу:
, (4.1)
приймаючи ν = 1,4 Гц.
Спочатку вибираємо за прототипом довжину ресори Lр=1,55м; орієнтовно можна приймати Lр = (0,35...0,45)L для задніх ресор автомобілів, де L – база автомобіля.
Потім із конструктивних міркувань установлюють коефіцієнти асиметрії ресори:
, (4.2)
де l1, l2 – розміри відповідно короткого й довгого кінців ресори l1+ l2 = Lр.
Змн. |
Арк. |
№ докум. |
Підпис |
Дата |
Арк. |
КП.А.АТ-091.19.ПЗ.ЧДТУ |

(4.3)
fдин = (0,7...0,9) fст= 0,8∙0,12=0,096м. (4.4)
(4.7)
Остаточно приймемо за ОН 8027–86 (табл. 10, додаток 4). b=70мм, h=15мм.
Довжину верхнього (корінного) листа ресори приймаємо за прототипом рівною Lp =1,55м. Відстань між стрем'янками lстр кріплення ресор вибирають конструктивно. Довжина решти листів визначається графоаналітичним методом. Для цього необхідно накреслити ресору в масштабі. Вона повинна мати форму балки рівного опору.
Рисунок 4.1- Розрахункова схема задньої підвіски
Рисунок 4.2- Характеристика пружних властивостей
Змн. |
Арк. |
№ докум. |
Підпис |
Дата |
Арк. |
КП.А.АТ-091.19.ПЗ.ЧДТУ |
Розроá. |
Савенчук В. В. |
Перевір. |
Хоменко И. М. |
Реценз. |
Н. Контр. |
Хоменко И. М. |
Затверд. |
5.Рульове управління |
Літ. |
Аркушів |
АТ-091 |
Для рульового керування визначають кінематичне і ω та силове іp передавальні числа:
, (5.1);
, (5.2);
Чисельне значення:
де αр.к, αк.к – кути повороту відповідно рульового й керованого коліс,
αр.к = 540...1080°, αк.к = 35...40°;
іωм і іωп, ір.м . і ір.п – кінематичне і силове передавальні числа відповідно рульового механізму і рульового приводу;
– сумарний момент опору повороту керованих коліс;
G= 8515 Н – вага, що припадає на керовані колеса;
f= 0,018– коефіцієнт опору коченню;
ц = 0,6...0,8 – коефіцієнт зчеплення шини з полотном дороги;
rковз = (0,12...0,15) rк – радіус ковзання шини, м;
rк – радіус кочення колеса, м (rк ≈ rст ≈ rд);
R = 0,2...0,25 м – радіус рульового колеса, м;
Mрк= Рр к ·R =350∙0.25=87,5 Н∙м – момент, який прикладається до рульового колеса;
С Р.к – зусилля, яке водій прикладає до рульового колеса, З; Необхідно виконання умови Рр.к ≤ 400 Н.
С – радіус повороту (радіус обкочування) керованого колеса, (довжина перепендикуляра, опущеного з центра п’ятна контакту шини з полотном дороги на подовження осі шворня).
Рульовий механізм
Необхідне зусилля на рульовому колесі
(5.3);
Чисельне значення:
Н
де ηр.м – 0,6...0,7 – ККД рульового механізму (прямий);
ηр.к = 0,85...0,95 – ККД рульового приводу.
Оскільки отримано при розрахунку 400Н > 124 Н необхідності встановлювати гідро підсилювач немає.
Рульовий привід
Значення кутів повороту керованих коліс автомобіля (без урахування кутів бокового уводу шин) знаходяться із залежності:
(5.4);
Змн. |
Арк. |
№ докум. |
Підпис |
Дата |
Арк. |
КП.А.АТ-091.19.ПЗ.ЧДТУ |
М – відстань між осями повороту керованих коліс (між осями шворнів);
L – база автомобіля.
Основні розміри рульової трапеції M, m, n визначаються за схемою на рисунку 5.1.
Рисунок 5.1 – Схема визначення геометричних розмірів трапеції
Для визначення величини М задаються довжиною поворотної цапфи (із конструктивних міркувань). При тороїдних шинах орієнтовно можна прийняти lц = Вш, де Вш – ширина профілю шини.
Кут и знаходимо за формулою:
(5.5);
Чисельне значення:
за умови, що m/n = 0,12...0,16.
Без урахування еластичності шин можна прийняти x = 0,7. Тоді
(5.6);
Чисельне значення:
м
Далі перевіряємо точність виконання залежності (5.4) за знайденими значеннями геометричних розмірів трапеції. Для цього в масштабі не менше ніж 1: 10 креслять схему рульової трапеції (рисунок 5.2). Потім, повертаючи одне з коліс (графічно) через 5° у межах можливого кута повороту, визначають кут повороту іншого колеса. Одержані дані заносимо у таблицю 5.1 і будуємо рисунок 5.2.
1,299 |
1,4 |

Рисунок 5.2 – Схема для визначення залежності між кутами повороту керованих коліс
Таблиця 5.1 – Кути повороту керованих коліс
Кути повороту колеса | Внутрішній αвн | |||||||
Зовнішній αз | теоретичний | 9,7 | 19,8 | 28,9 | 38,5 | 47,4 | 56,8 | 65,37 |
графічний | 9,3 | 19,5 | 28,2 | 37,8 | 47,1 | 55,7 | 65,7 |
Теоретичні значення α з обчислюємо за виразом (5.4). Далі за даними таблиці 5.1 будуємо графіки залежності α з = f(αвн) (рисунок 5.3).
αз |
αвн |
Змн. |
Арк. |
№ докум. |
Підпис |
Дата |
Арк. |
КП.А.АТ-091.19.ПЗ.ЧДТУ |
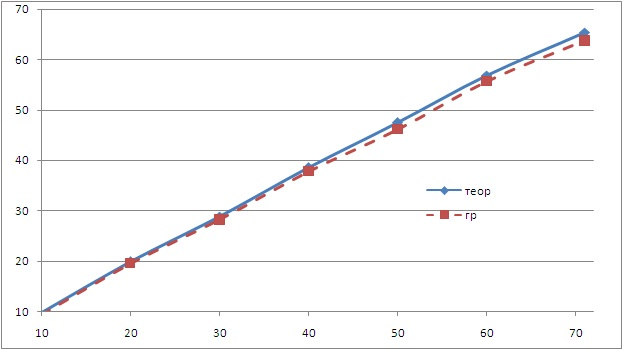
Рисунок 5.3– Залежність між кутами повороту керованих коліс автомобіля
Геометричні параметри рульової трапеції вважають задовільними, якщо при повороті коліс на кут до 20° графічна та теоретична залежності збігаються (відхилення не перевищує 2... 3°).
Гальмівна система
Гальмовий механізм
Граничні значення моменту тертя гальмового механізму Мтр повинні відповідати значенн
Изм. |
Лист |
№ докум. |
Подпись |
Дата |
Лист |
КП.А.АТ-091.19.ПЗ.ЧДТУ ВКРБ.АТ.081-12.ПЗ.ЧДТУ ВКРБ.АТ.081-12.ПЗ.ЧДТУ |
Разраб. |
Савенчук В.В. |
Провер. |
Хоменко І.М. |
Н. Контр. |
Хоменко І.М. Кальченко В.В. |
Утверд. |
6. Гальмова система |
Лит. |
Листов |
АТ-091 |
Граничне значення Мτ визначаємо умовами взаємодії колеса з полотном дороги:
, (6.1)
де - розрахункове значення коефіцієнта зчеплення,
, (6.2)
де Кτ - коефіцієнт розподілу гальмових сил Рτ1 і Рτ2 між колесами відповідно передньої та задньої осей;Кτ = 0,9…1.
a, b, hg - координати центра мас.
.
Вертикальні опорні реакції дороги на передній Zτ1 і задній Zτ2 осях автомобіля визначаємо за формулами:
;
; (6.3)
де Gа - повна вага автомобіля,Н;
L - база автомобіля, м;
Zτ - вертикальна реакція полотна дороги, Н.
H,
H.
Граничні значення гальмових моментів на колесах:
При гальмуванні стоянковим гальмом лише задніх коліс автомобіля гальмовий момент становить:
(6.4)
де α ≈ 9,10 (ухил 16%) - кут ухилу, на якому повинен бути загальмований автомобіль.
Гальмовий привід
Вибір типу і конструкції гальмового приводу базується на дотриманні умови повного узгодження мінімального часу і плавності спрацювання, необхідного розподілу гальмових сил між колесами автомобіля, зручності та легкості керування, довговічності й простоти конструкції.
Для забезпечення надійності роботи приводу робочої гальмової системи його конструкція повинна мати не менше двох контурів. Стоянкова гальмова система має конструкцію, яка дозволить використовувати її як запасну.
Після вибору типу визначаємо конструкцію основних механізмів і пристроїв гальмового приводу (головного гальмового циліндра, колісних циліндрів, гальмового крана, гальмового циліндра або камери, пружинного енергоакумулятора тощо).
Потім знаходимо кінематичне іk передавальне число:
(6.5)
де Sпед.роб – робочий хід педалі або важеля гальма (Sпед.роб = 80...100 мм для вантажних автомобілів, 70...75 мм – для легкових);
ΣSк – сумарне переміщення
Змн. |
Арк. |
№ докум. |
Підпис |
Дата |
Арк. |
КП.А.АТ-091.19.ПЗ.ЧДТУ ВКРБ.АТ.081-12.ПЗ.ЧДТУ |
Сили які розтискають колодки гальмового механізму, зображені на рисунку 6.1.
Рисунок 6.1 – Схема сил які розтискають колодки гальмового механізму
Зусилля яке повинен прикладати водій до педалі автомобіля:
Р1= Р2=Р; (6.6)
(6.7)
Підставивши значення,отримаємо:
Н·м
де Р1,Р2,– приводні сили;
Rб = 0,38 м – робочий радіус гальмового барабана (визначається із можливості розміщення барабана в середині ободу колеса);
а,b,h – геометричні розміри гальмового барабану (а = b =0.8Rб);
= 0,3 – коефіцієнт тертя.
Сили, прикладені до колодок передніх і задніх коліс:
Н (6.8)
Н
Н (6.9)
Н
Н (6.10)
Изм. |
Лист |
№ докум. |
Подпись |
Дата |
Лист |
КП.А.АТ-091.19.ПЗ.ЧДТУ ВКРБ.АТ.081-12.ПЗ.ЧДТУ |
- питоме навантаження на гальмівні накладки.
- питома робота тертя.
1. Питоме навантаження на гальмівні накладки:
(6.11)
де: - сумарна площа гальмівних накладок робочої системи,
- вага автомобіля.
Чисельне значення:
Н/см2
2. Питома робота тертя:
(6.12)
де: ; А=18100·372/2=1238945 Дж– кінетична енергія автомобіля при максимальній швидкості, враховуючи, що вона повністю поглинається гальмівними механізмами.
Чисельне значення:
Від питомої роботи залежить знос і нагрівання елементів гальмівного механізму - гальмівного барабана.
Для зменшення питомої роботи необхідно збільшити площу гальмівних накладок і відповідно ширину гальмівних барабанів і їх діаметр.
При збільшенні розмірів гальмівного барабана йде збільшення поверхні охолодження, що сприятливо позначається на режимі гальмування. Цим пояснюється останнім часом тенденція збільшення розміру коліс автомобілів (особливо легкових) для можливості розміщення гальмівних барабанів збільшеного розміру.
Нагрівання гальмівного барабана (диска) за одне гальмування:
(6.13)
де: – маса автомобіля, яка припадає на колесо, що гальмує приходящаяся на тормозящее колесо
mб – маса гальмівного барабана
С»500 Дж/(кг. К) – питома теплоємність чавуну і сталі
Чисельне значення:
За вимогами до гальмівним механізмам нагрівання гальмівного диска за одне гальмування не повинен перевищувати 20 С.
Визначимо максимальні моменти тертя переднього і заднього гальм автомобіля, виходячи з умови повного використання зчеплення шин з дорогою:
M1=(φּrּМּg/(n1ּL))ּ(b+φּh), Нּм, (8.14)
M2=(φּrּМּg/(n2ּL))ּ(a-φּh), Нּм, (8.15)
де М1 і М2 – максимально можливі моменти тертя передніх і задніх гальм відповідно в разі одночасного гальмування всіма колесами автомобіля;
φ – коефіцієнт зчеплення шини з дорогою, φ=0,8;
r – радіус кочення колеса, r=0,29 м
М – маса автомобіля, М=1845 кг
а = 1,48 м, b = 1,32 м, h = 0.75 м – координати центра мас автомобіля;
L - база автомобіля, L = 2,8 м;
n1, n 2 – число коліс з гальмами на передній і задній осях.
Як видно з розрахунків, момент тертя на задніх колесах менше ніж на передніх.
Ефективність гальмі оцінюється гальмівним шляхом і встановленим загальмовуванням. Прирівнявши силу інерції автомобіля і сумарну гальмівну силу знайдемо вираз для встановленого загальмовування:
j = φ • g = 0.8 • 9.81 = 7.848 м/с2, (6.16)
Максимально можливий шлях гальмування з початковою швидкістю 90 км/год розраховується за формулою:
Изм. |
Лист |
№ докум. |
Подпись |
Дата |
Лист |
КП.А. АТ.091 - 19.ЧДТУ ВКРБ.АТ.081-12.ПЗ.ЧДТУ |
де S – гальмівний шлях, м;
V0 – початкова швидкість гальмування, м/с
V0 =90 км/год=25 м/с.
S=0,125·37+37·37/(2·7,848)=88 м.
Отриманий вираз справедливий для випадку одночасного гальмування передніми і задніми колесами автомобіля.