Ионно-плазменное травлениеповерхности подложек происходит за счет ее бомбардировки положительными ионами. При этом энергия ионов должна превышать энергию связи атомов обрабатываемого материала (~60 эВ для ). Следует так же учитывать, что скорости ионного травления самых различных веществ отличаются мало.
Для бомбардировки используются ионы инертных газов, доставляемые посредством дрейфа в электрическом и/или электромагнитном поле из области тлеющего разряда. Тлеющий разряд зажигается между анодом и катодом при давлении инертного газа около 6,67 Па. При этом наличие специального анода необязательно, поскольку его роль могут играть заземленные части установки. Катодом служит само обрабатываемое вещество. Ионы должны падать перпендикулярно поверхности катода, чтобы исключить боковое подтравливание.
Побочным эффектом бомбардировки являются радиационные нарушения. В случае малых ускоряющих напряжений (до 1,5 кВ) их роль мало заметна.
Для ионного травления используется источник мощностью до 1 кВт при рабочей частоте 13,56 МГц. При этом на катоде может располагаться до 10 кремниевых пластин. Прикладываемое к электродам напряжение может быть постоянным или переменным. Используя переменные ускоряющие напряжения с частотой порядка 10-20 МГц, можно травить практически любые материалы. Таким образом, имеется возможность селективной обработки пластин как при фотолитографии.
Управление скоростью обработки достигается изменением подводимой мощности. Для малых плотностей мощности характерна линейная зависимость скорости травления, которая позволяет наиболее точно регулировать количество удаляемого вещества:
Рис. 4.5. Параметры ионного травления SiО2:
а) зависимость удаляемого слоя h от времени травления t при T=190°C в Ar;
б) скорость травления V тр в зависимости от удельной мощности P
при U уск = 1200 В
Ионное травление обеспечивает удаление слоев вещества с точностью до 30 нм. Высокая разрешающая способность метода позволяет использовать его при получении рисунка схем в процессах фотолитографии. При плотностях ВЧ-мощности свыше 2,5 Вт/см2 скорость травления растет быстрее из-за нагрева обрабатываемой поверхности и линейная зависимость нарушается. Сильное влияние на скорость травления оказывает участие в процессе активных газов – кислорода и водорода. При добавлении 10% любого из этих газов скорость травления органических веществ, в частности фоторезистов, возрастает, а неорганических – падает, т.е. селективность обработки увеличивается. Увеличение скорости травления органических веществ объясняется тем, что к ионному травлению добавляется химический процесс.
Итак, основным достоинством ионного травления является универсальность. Данный метод можно применять для обработки широкого диапазона материалов и при сравнительно небольшой температуре (100-200°С). Ионное травление может быть использовано для травления многослойных структур, несовместимых с точки зрения жидкостной и термохимической обработки. Уникальной особенностью ионного травления является отсутствие подтравливания при создании локальных углублений.
Есть у метода ионно-плазменного травления и недостатки. Одним из них является селективность, т.е. в результате стравливания слоя оксида кремния вместе с ним может быть удален и поверхностный слой кремния (подложки).
Глава 5. ДИЭЛЕКТРИЧЕСКИЕ ПЛЕНКИ В ИС. МЕТОДЫ ИХ ПОЛУЧЕНИЯ. ТЕХНОЛОГИИ ИЗГОТОВЛЕНИЯ ГИБРИДНЫХ ИС
5.1. Конструктивно-технологические функции диэлектрических плёнок
Создание, развитие и широкое внедрение в промышленность планарной технологии в кремниевых ИС в значительной мере обязаны тому, что на поверхности кремния можно сформировать диэлектрическую пленку, обладающую прекрасными маскирующими свойствами. Для этого наиболее распространенным и качественным диэлектриком остается диоксид кремния.
Использование окисленной поверхности кремния в качестве маски обусловлено химической инертностью диоксида кремния SiO2 по отношению ко многим реагентам. Достаточно сказать, что пленка SiO2 растворима только в плавиковой кислоте и концентрированных растворах щелочей. Однако роль таких пленок не исчерпывается их применением в качестве масок при формировании элементов ИС и защиты этих элементов от влияния внешних воздействий (примесей, влаги, излучения и т.п.) Диэлектрические пленки служат также для электрической изоляции отдельных приборов и коммутационных проводников (особенно многослойных) в ИС.
В зависимости от функций, выполняемых диэлектрическими пленками, к ним предъявляют различные требования. Например, пленки, применяемые в качестве масок, должны обеспечивать:
· селективность по отношению к тем или иным технологическим факторам (к растворам, облучению, газам, плазме и т.п.);
· отсутствие пор и трещин;
· равномерность толщины, структуры физико-химических свойств по площади и глубине маски;
· хорошую адгезию к пластине.
Если диэлектрическая пленка применяется в качестве изоляции, то её основными характеристиками являются:
· удельное электросопротивление;
· тангенс угла диэлектрических потерь (tg δ);
· диэлектрическая проницаемость (ε);
· равномерность и стабильность этих свойств.
5.2. Формирование плёнок SiO2 термическим окислением кремния
Наиболее широко применяемым методом формирования плёнок SiO2 является окисление кремния при высоких температурах - термическое окисление.
Плёнки SiO2 толщиной 0,5–1 нм легко образуются уже при комнатной температуре, и такая тонкая пленка оказывается весьма устойчивой. Соответственно при высоких температурах (~1200°C) эта аморфная плёнка кристаллизуется. Переходу из аморфного состояния в кристаллическое способствуют центры кристаллизации, созданные примесями и несовершенством структуры.
В результате реакции кремния с кислородом или водой образуется так называемый термический оксид кремния:
. (5.1)
. (5.2)
Заметим, что скорость реакции (5.2) выше, чем скорость реакции (5.1).
В отличие от термических, анодными диоксидами называются такие, которые получаются в жидком электролите или плазме за счет реакции ионов, движущихся под действием электрического поля:
, (5.3)
где - положительный заряд от внешнего источника.
После образования первого слоя SiO2 на поверхности кремния дальнейший рост диоксида может протекать по двум механизмам:
а) диффузия кислорода через поверхностный слой SiO2 к поверхности кремния и реакция на этой поверхности с образованием нового монолитного слоя SiO2;
б) к поверхности диоксида диффундирует кремний и окисляется кислородом.
Однако следует заметить, что второй механизм не играет существенной роли в процессе окисления, так как скорость диффузии кремния в диоксидах на несколько порядков меньше скорости диффузии кислорода.
Таким образом, механизм окисления кремния складывается из нескольких последовательных стадий:
а) диффузии кислорода (или другого окислителя) из газового потока к поверхности кремниевой пластины;
б) адсорбции кислорода этой поверхностью;
в) реакции окисления кремния согласно уравнениям и образования первоначального слоя SiO2;
г) диффузии окислителя через этот слой к поверхности кремния Si, где и протекает следующая реакция окисления.
Рис.5.1. Схема процесса последовательного окисления Si
Самой медленной из указанных стадий является диффузия кислорода через слой диоксида. Следовательно, она и будет лимитировать скорость процесса в целом.
Для стационарного процесса скорости потоков кислорода во всех стадиях должны быть равны. Поскольку адсорбция происходит мгновенно, то j 1 = j 2 = j 3 , где j 1– скорость массопередачи кислорода из газового потока к поверхности пластины; j 2 – диффузии кислорода через окисленный слой к поверхности кремния; j 3– скорость реакции окисления Si.
Согласно закону Фика, для потока окислителя можно записать:
j 2 , (5.4)
где D – коэффициент диффузии окислителя в слое диоксида; ,
– соответственно концентрации О2 на поверхности пластины (SiO2) и границе раздела ″кремний-диоксид″;
– толщина слоя диоксида (формально глубина диффузии).
Скорость взаимодействия кремния с кислородом по уравнению (5.1) описывается реакцией первого порядка:
j 3 , где k – постоянная скорости реакции окисления кремния.
Поскольку для стационарного процесса j 2 = j 3 , то
. (5.5)
Для потока окислителя, достигающего поверхность раздела между диоксидом и кремнием:
, (5.6)
где – число молекул окислителя в единицу объёма диоксида,
– скорость роста диоксида.
Пусть при t = 0 . Величина
– есть толщина диоксида, полученного при предыдущем акте окисления, то есть окисление осуществляется в несколько этапов. Тогда из (5.6) следует
, (5.7)
где ;
.
Решая эту систему, получаем:
. (5.8)
Уравнение имеет два предельных случая:
1. Время окисления велико: , где В = const – постоянная параболического закона окисления.
2. Время окисления мало: , где В/А = const – постоянная линейного закона окисления.
|
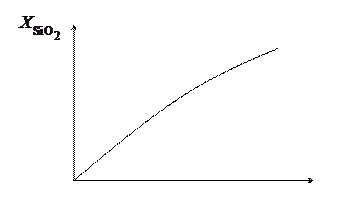
Рис. 5.2. Экспериментальная зависимость толщины
оксида кремния от времени окисления
|
Рис. 5.3. Экспериментальная зависимость параметра В от температуры
Рассмотренная модель термического окисления справедлива как для окисления в чистом ″сухом″ кислороде, так и в чистых парах воды. На практике при термическом окислении обычно используется смесь кислорода и паров воды.
Следует отметить, что количественный анализ процесса окисления во влажном кислороде довольно сложен из-за большого числа возможных реакций в системе и одновременной диффузии в оксидном слое двух окислителей – кислорода и водяных паров. Кроме того, пленки SiO2, полученные в парах воды и во влажном кислороде, обладают худшими электрическими и защитными свойствами, чем пленки, полученные в ″сухом″ кислороде.
Химическое осаждение диэлектрических пленок из газовой фазы наиболее распространено на практике вследствие простоты, универсальности и высокой производительности процесса. Простота процесса объясняется простотой оборудования и доступностью (недефицитностью) исходных материалов, универсальностью (возможностью осаждать пленки различных материалов), высокой производительностью (значительно большей скоростью химических реакций осаждения по сравнению с процессом окисления).
Для окисления пленок SiO2 используются следующие реакции:
(1) – пиролиз (T = 600-8000С, R – органические радикалы, например C2H5, CH3);
(2) – окисление (Т = 250-4000С);
(3) – гидролиз (Т = 200-2500С).
Для получения SiO2-пленок по реакции пиролиза могут использоваться и другие этоксилианы, представляющие собой продукты замещения в молекуле SiH4 атомов водорода на группу OC2H5. При этом степень замещения может изменяться от 0 до 4. Скорость роста пленок SiO2 по такому методу замещения при Т >700°C достаточно велика, что позволяет получать слои достаточно высокого качества толщиной в несколько микрон всего за 10-15 минут.
Использование температур ниже 700°С не рекомендовано, поскольку в этом случае пиролиз оказывается неполным и, как правило, пленки SiO2 оказываются загрязненными промежуточными продуктами разложения, которые содержат неконтролируемые донорные и акцепторные примеси.
В отличие от реакции пиролиза (1), реакции окисления (2) и гидролиза (3) протекают без органических остатков и в результате формируются очень чистые пленки. Вместе с тем низкие температуры также крайне не желательны. Поэтому основным требованием к реакциям окисления и гидролиза является жесткий контроль температуры и регулировка концентрации газовой фазы на поверхности пластин.
Обычно скорость роста пленки растет линейно с увеличением скорости потока силана. Однако при повышении температуры скорость осаждения SiO2 растет очень резко и практически неконтролируемо. Поэтому производят разбавление газа, например кислородом, и тогда зависимость скорости роста SiO2 от скорости потока силана принимает следующий вид, показанный на рис. 5.4:
Рис. 5.4. Зависимость скорости роста пленки SiO2 с увеличением
скорости потока газа (силана SiН4)
Процесс, описываемый реакцией гидролиза (3), начинает протекать уже при комнатной температуре, и образующийся в парах диоксид кремния осаждается на поверхность в виде достаточно рыхлых образований. Как и в предыдущем случае, необходимо поддерживать температуру на уровне 500-5500С и подавать пары SiCl4 (SiF4) непосредственно на поверхность пластины.
Достоинством процесса осаждения слоев SiO2 по реакциям окисления (2) и гидролиза (3) является возможность их сочетания с эпитаксиальным наращиванием кремния в одном аппарате и высокая чистота формируемых пленок.
Помимо оксида кремния в технологии ИС используются нитрид кремния Si3N4, оксид алюминия Al2O3, диоксид TiO2, пятиокись тантала Ta2O5. Например, формирование пленок Si3N4 прямым азотированием пластин кремния практически не применяется из-за высоких температур (~13000С) процесса и чрезвычайно малых скоростей формирования пленок.Как и при создании слоев SiO2, наилучшие результаты получаются при использовании газофазных реакций.
Слои оксида алюминия обычно получают анодным окислением алюминия или осаждением Al2O3 из металлоорганических соединений алюминия, как и в случае SiO2.