При получении отливок в песчано-глинистые и холодно-твердеющие смеси необходимо учесть следующие правила.
Расположения отливки в форме (рис. 1.4). Когда заготовка имеет длину больше её поперечного сечения, то целесообразно располагать её горизонтально (рис. 1.4, б), что позволяет экономит формовочный материал, а также при таком расположении заготовки, при заливке расплава происходит выравнивание механических свойств по сечению отливки из-за малого влияния ликвации по удельному весу.
а б
Рисунок 1.4. Варианты литейной формы:
а – с вертикальным, б – с горизонтальным расположением оси отливки
Вертикальное расположение оси пустотелой отливки в форме предпочтительнее при размерах, когда поперечное сечение заготовки гораздо больше длины. При этом стержень, формирующий полость или отверстие в отливке, может иметь 2 и более точек опоры (рис. 1.5, б), т.е. занимает более устойчивое положение в форме, чем при горизонтальном расположении оси (рис. 1.5, а).
а б
Рисунок 1.5. Варианты расположения пустотелой отливки
а – с двумя точками опоры, б – с тремя точками опоры
Детали, у которых один габаритный размер гораздо больше других, целесообразно располагать так, чтобы максимальный размер лежал в горизонтальной плоскости, как показано на рисунке 1.6, а. Детали с примерно одинаковыми габаритными размерами можно располагать как вертикально (рис. 1.6, б), так и горизонтально (рис. 1.6, в).
а б в
Рисунок 1.6. Варианты расположения отливки в литейной форме
Также при выборе плоскости разъёма наиболее ответственные поверхности отливки целесообразно располагать в нижней части формы или вертикально, так как в верхней части отливки скапливаются дефекты – газовые раковины и шлаковые включения. Плоскость разъёма выбирают с учётом удобства формовки и извлечения модели из формы. Кроме того, желательно, чтобы отливка или, по крайней мере, её базовые поверхности для механической обработки были расположены в одной полуформе.
а |
г |
в |
б |

Рисунок 1.7. Эскизы деталей: а) стальной; б) чугунной
Эскизы отливок: в) стальной; г) чугунной, где: 1 – разъём модели; 2 – припуск на механическую обработку; 3 – стержень; 4 – формовочные уклоны; 5 – необрабатываемые отверстия
Правило параллельных лучей. От расположения модели будет зависеть конфигурация внешних обводов. При изготовлении детали сложной конфигурации с ребрами (рис. 1.8), для извлечения модели из формы, по правилу параллельных лучей, части отливки не должны давать затенённых участков при направлении лучей снизу и сверху. Это правило также называют методом теневого рельефа. На рисунке 1.8, а показана недопустимая формовка, в виду невозможности извлечения модели из формовочного материала. Для этой отливки необходимо или изменить конфигурацию рёбер – сделать их параллельными лучам (рис. 1.8, б), или поменять расположение отливки на вертикальное.
а б
Рисунок 1.8. Использование правила параллельных лучей
Назначение напусков в «теневых» участках позволяет упростить технологическую оснастку, технологию изготовления и в конечном итоге получить более качественные отливки (рис. 1.9).
б |
а |
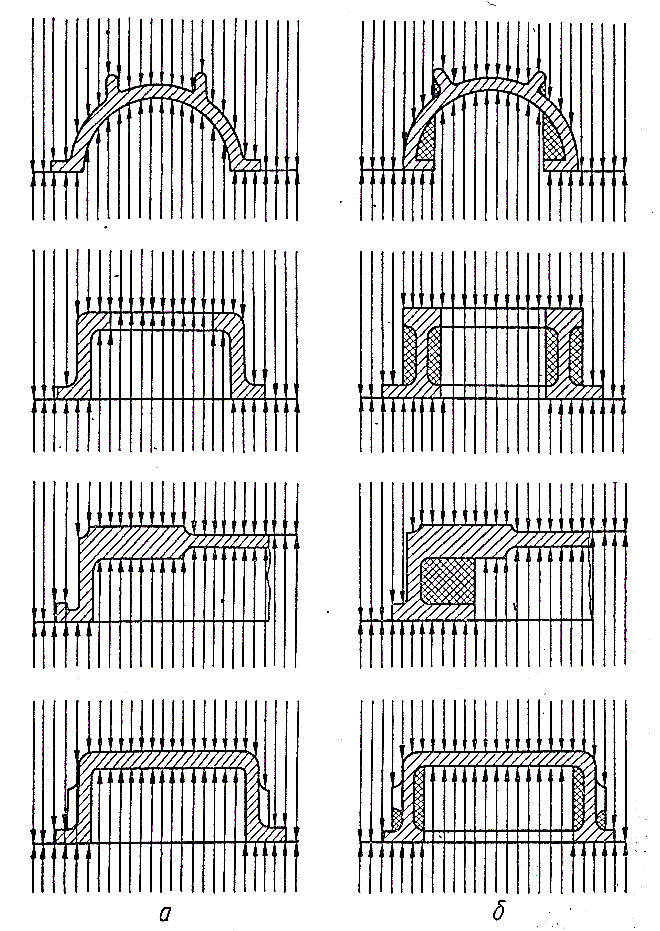
Рис. 1.9. Определение напусков методом «теней»
а – напуски не требуются; б – напуски необходимы (заштрихованные участки)
Назначения галтелей. Толщина стенок литых деталей назначается, исходя из требуемой расчётной прочности с учётом жидкотекучести металла. При сопряжении стенок применяют галтели (радиусы внутренних закруглений), они применяются для предупреждения образования трещин в углах сопряжения стенок.
Для одновременного затвердевания толщину внутренних стенок рекомендуется делать равной примерно 0,8S (где S - толщина наружных стенок).
Переходы от стенки к стенке следует выполнять с галтелями (рис. 10). При сопряжении стенок под углом (рис. 1.10 а) вследствие встречи линий теплового потока во внутреннем угле соединения образуется горячий узел, замедляющий остывание. Кроме того, такое соединение затрудняет заполнение формы металлом и препятствует усадке.
R в |

а б
Рисунок 1.10. Галтели при сопряжении стенок разной толщины
Радиус галтели (рис. 1.10, а) рассчитывается по формуле:
Соотношение толщин сопрягаемых стенок отливки не должно превышать двух.
При угловых сопряжениях стенок для получения плавного перехода делают скругление с внешним радиусом (рис. 1.10, б), рассчитанным по формуле:
Найденные из приведенных ориентировочных соотношений радиусы округляют до ближайших стандартных размеров (R = 1, 2, 3, 5, 8, 10, 15, 25, 30, 40 мм). Так как небольшое изменение радиусов сопряжений мало влияет на качество отливки, то рекомендуется унифицировать радиусы.
Назначение стержней и болванов. Внутренние полости и отверстия изготавливают с помощью стержней и «болванов». Внешняя конфигурация стержней повторяет внутренние обводы полости отливки. Стержни изготавливаются в стержневых ящиках. Болваны заложены в конфигурацию модели.
Для образования полостей сложной конфигурации применяют сборные стержни, состоящие из нескольких простых частей (рис. 1.11, а).
Однако, большое количество в форме стержней нежелательно. Если есть возможность вместо двух стержней 1 – горизонтального и 3 – вертикального (рис. 1.11, а) использовать один стержень 1 (рис. 1.11, б). Увеличение количества стержней усложняет и удорожает технологический процесс изготовления литейной формы и снижает точность отливки. [1].
а б
Рис. 1.11 Применение правила минимума стержней:
а – сборный стержень – нетехнологично; б – цельный стержень – технологично;
стержни: 1–горизонтальный, 3 – вертикальный; 2 – жеребейка
Стержни, применяемые при изготовлении глухих полостей отливки, имеют всего одну опору, и поэтому могут потерять устойчивость. При сборке они могут упасть в полость формы, что приведёт к засорению расплава и нарушению конфигурации формы. Для устойчивости одноопорных стержней изготавливается жеребейка 2 (искусственная опора), которая устанавливается между стержнем 1 и стенками формы (рис. 1.11 а).
Рисунок 1.12. Применение жеребейки в литейной форме
Жеребейка – металлический стержень, имеющий химический состав, близкий по составу к сплаву, из которого отливается деталь (рис. 1.12). Применение жеребеек крайне нежелательно, так как они являются источниками образования дефектов в отливках (газовые раковины, несвариваемость).
Иногда для получения глухих (несквозных) отверстий вместо стержней применяют «болваны» рисунок 1.13. Они дают возможность изготавливать форму без стержней, выполняя их функции.
Рисунок 1.13. Применение «болванов» для выполнения полостей отливки
Болван – часть модельного комплекта (модели), не выступающая за плоскость разъёма. Высота внутренней полости - H, выполняемой «болваном» в нижней части формы не должна превышать ширину – B или диаметр её сечения H £ B (рис. 1.13). Если же внутренняя полость выполняется «болваном» в верхней части формы, то h £ 0,3× b где h – высота верхней полуформы и b – ширина или диаметр её сечения.
Минимальный диаметр отверстий, выполняемых литьем, выбирают так, чтобы избежать сильного перегрева и пригара стержня к стенкам отверстия. Минимальные диаметры отливаемых отверстий в зависимости от материалов и способов литья:
При литье в ПГС:
чугун: dmin 10 мм при глубине отверстия глухого – l £3 d, сквозного – l£6 d
сталь dmin: 15…20 мм при глубине отверстия глухого – l £3 d, сквозного – l £6 d
При литье в оболочковые формы:
сталь и чугун: dmin 8…10 мм при глубине отверстия глухого – l £5 d, сквозного – l £10 d
При литье в кокиль:
чугун: dmin 10 мм при глубине отверстия глухого – l £2 d, сквозного – l £3 d
сталь dmin: 12 мм при глубине отверстия глухого – l £2 d, сквозного – l £3 d
При литье по выплавляемым моделям:
сталь, чугун dmin: 6 мм при глубине отверстия глухого – l £2 d, сквозного – l £3 d
При литье под давлением:
алюминиевые сплавы: dmin: 2…3 мм при глубине отверстия глухого – l £4 d, сквозного – l £8 d.
В общем случае при литье мелких и средних отливок из чугуна в песчаные формы не рекомендуется выполнять отверстия литьем, если их диаметры не превышают следующих значений:
- при массовом производстве – 20 мм;
- при серийном производстве – 30 мм;
- при индивидуальном производстве – 50 мм.
На мелких и средних отливках из чугуна при литье в песчаные формы выполняют литьем уступы шириной более 25 мм и выемки глубиной выше 6 мм.
Положение стержня должно быть строго зафиксировано в полости формы. Для этого предусматриваются стержневые знаки, как продолжения отверстий. В местах отверстий – 1 у детали (рис. 1.14, а), модель имеет выступающие части для получения в форме так называемых литейных знаков – 2 (рис. 1.14, б).
а б
Рисунок 1.14. Деталь и литейная форма для её получения
В зависимости от положения стержня при сборке литейной формы стержневые знаки подразделяются на горизонтальные (рис. 1.15 а) и вертикальные (рис. 1.15 б) ГОСТ 3212-92.
б |
а |

Рисунок 1.15 Стержневые знаки горизонтальные – а и вертикальные – б.
Длина горизонтальных знаков должна соответствовать указанным:
для форм «по-сырому» – в табл. 1.2,
для форм «по-сухому» – в табл. 1.3,
для форм, твердеющих в контакте с оснасткой – в табл. 1.4.
Таблица 1.2.
Длина горизонтальных знаков для форм «по-сырому», мм
| Длина знака l, не более при длине стержня L | |||||||||
До 40 | Св. 40 до 63 | Св. 63 до 100 | Св. 100 до 160 | Св. 160 до 250 | Св. 250 до 400 | Св. 400 до 630 | Св. 630 до 1000 | Св. 1000 до 1600 | Св. 1600 до 2500 | |
До 25 | 20 | 25 | 30 | 35 | - | - | - | - | - | - |
Св. 25 до 40 | 45 | 50 | ||||||||
Св. 40 до 63 | 40 | 50 | 60 | 75 | 95 | |||||
Св. 63 до 100 | 35 | 45 | 55 | 65 | 85 | 105 | ||||
Св. 100 до 160 | 35 | 40 | 50 | 60 | 75 | 95 | 115 | 130 | ||
Св. 160 до 250 | 40 | 65 | 80 | 100 | 125 | 145 | ||||
Св. 250 до 400 | 40 | 45 | 60 | 75 | 85 | 110 | 140 | 160 | 180 | |
Св. 400 до 630 | 65 | 85 | 100 | 130 | 160 | 180 | 220 | |||
Св. 630 до 1000 | - | - | - | - | - | 115 | 150 | 180 | 210 | 260 |
Св. 1000 до 1600 | - | - | 200 | 245 | 300 |
Таблица 1.3
Длина горизонтальных знаков для форм «по-сухому», мм
| Длина знака l, не более при длине стержня L | |||||||||||
До 40 | Св. 40 до 63 | Св. 63 до 100 | Св. 100 до 160 | Св. 160 до 250 | Св. 250 до 400 | Св. 400 до 630 | Св. 630 до 1000 | Св. 1000 до 1600 | Св. 1600 до 2500 | Св. 2500 до 4000 | Св. 4000 | |
До 25 | 15 | 20 | - | - | - | - | - | - | - | - | - | - |
Св. 25 до 40 | 20 | 25 | 30 | 35 | 40 | |||||||
Св. 40 до 63 | 50 | |||||||||||
Св. 63 до 100 | 25 | 30 | 35 | 40 | 45 | 55 | 65 | |||||
Св. 100 до 160 | ||||||||||||
Св. 160 до 250 | 30 | 35 | 40 | 50 | 55 | 60 | 70 | 75 | ||||
Св. 250 до 400 | 35 | 40 | 45 | 90 | ||||||||
Св. 400 до 630 | - | 45 | 50 | 55 | 60 | 65 | 75 | 90 | 110 | 120 | 130 | |
Св. 630 до 1000 | - | 55 | 60 | 65 | 70 | 80 | 100 | 130 | 150 | 160 | 170 | |
Св. 1000 до 1600 | - | 65 | 70 | 80 | 90 | 120 | 150 | 180 | 200 | 220 | ||
Св. 1600 до 2500 | - | 75 | 90 | 100 | 130 | 170 | 210 | 240 | 270 | |||
Св. 2500 до 4000 | - | 95 | 120 | 145 | 180 | 220 | 250 | 300 | ||||
Св. 4000 | - | 125 | 150 | 190 | 230 | 270 | 320 |
Таблица 1.4
Длина горизонтальных знаков для форм, твердеющих в контакте с оснасткой, мм
| Длина знака l, не более при длине стержня L | |||||||||||
До 40 | Св. 40 до 63 | Св. 63 до 100 | Св. 100 до 160 | Св. 160 до 250 | Св. 250 до 400 | Св. 400 до 630 | Св. 630 до 1000 | Св. 1000 до 1600 | Св. 1600 до 2500 | Св. 2500 до 4000 | Св. 4000 | |
До 25 | 10 | 15 | 20 | 25 | - | - | - | - | - | - | - | - |
Св. 25 до 40 | 30 | 35 | ||||||||||
Св. 40 до 63 | 40 | |||||||||||
Св. 63 до 100 | 15 | 20 | 30 | 30 | 35 | 40 | 45 | 50 | ||||
Св. 100 до 160 | ||||||||||||
Св. 160 до 250 | 20 | 25 | 35 | 40 | 45 | 50 | 55 | |||||
Св. 250 до 400 | 25 | 30 | 35 | 40 | 45 | 50 | 55 | 60 | 70 | |||
Св. 400 до 630 | - | - | 40 | 45 | 50 | 55 | 60 | 70 | 90 | 100 | 120 | |
Св. 630 до 1000 | 60 | 65 | 80 | 105 | 130 | 145 | 160 | |||||
Св. 1000 до 1600 | 55 | 65 | 75 | 90 | 110 | 150 | 165 | 185 | ||||
Св. 1600 до 2500 | - | 50 | 60 | 70 | 80 | 95 | 135 | 165 | 185 | 205 | ||
Св. 2500 до 4000 | - | - | 75 | 85 | 105 | 140 | 180 | 210 | 230 | |||
Св. 4000 | - | 95 | 110 | - |
При количестве знаков более двух длина их должна быть уменьшена на 30-50% по сравнению с указанными в таблице 1.2-1.4.
Высоту нижних вертикальных знаков для всех видов смесей (рис.1.15) следует назначать в соответствии с табл.1.5.
Таблица 1.5
Высота нижних вертикальных знаков, мм
| Длина знака h, не более при длине стержня H | ||||||||||
До 40 | Св. 40 до 63 | Св. 63 до 100 | Св. 100 до 160 | Св. 160 до 250 | Св. 250 до 400 | Св. 400 до 630 | Св. 630 до 1000 | Св. 1000 до 1600 | Св. 1600 до 2500 | Св. 2500 | |
До 25 | 20 | 30 | 30 | 30 | - | - | - | - | - | - | - |
Св. 25 до 40 | 50 | 60 | |||||||||
Св. 40 до 63 | 25 | 35 | 35 | 35 | 40 | 80 | 110 | 130 | |||
Св. 63 до 100 | 50 | ||||||||||
Св. 100 до 160 | 30 | 70 | 100 | 130 | |||||||
Св. 160 до 250 | 180 | ||||||||||
Св. 250 до 400 | 40 | 60 | 80 | 120 | 180 | 190 | |||||
Св. 400 до 630 | 40 | 40 | 40 | 40 | 40 | 50 | 120 | 170 | 180 | ||
Св. 630 до 1000 | 50 | 50 | 50 | 50 | 50 | 50 | 50 | 70 | 110 | 150 | 160 |
Св. 1000 до 1600 | 70 | 70 | 70 | 70 | 70 | 70 | 70 | 70 | 100 | 130 | 140 |
Св. 1600 до 2500 | 100 | 100 | 100 | 100 | 100 | 100 | 100 | 100 | 100 | 110 | 120 |
Св. 2500 | 110 | 110 | 110 | 110 | 110 | 110 | 110 | 110 | 110 | 110 | 110 |
При соотношении L/D или
нижний знак рекомендуется выполнять в соответствии с рисунок 1.16.
Рисунок 1.16
Высоту верхнего вертикального знака следует принимать не менее 0,5 от высоты нижнего знака.
Для массового и крупносерийного производства допускается назначать высоту нижнего и верхнего знаков одинаковыми.
Назначение уклонов. Для облегчения удаления модели из формы ее боковые поверхности изготавливают с литейными (формовочными) уклонами (рис. 1.17). Литейные уклоны определяются углом β в градусах или размером в миллиметрах.
£ 3° |

Рисунок 1.17. Применение формовочных уклонов
Формовочные уклоны следует выполнять для поверхностей (рис. 1.18):
- на обрабатываемых поверхностях отливки сверх припуска на механическую обработку за счет увеличения размеров отливки (рис. 1.18, а) «с плюсом». Допускается выполнение уклонов за счет уменьшения припуска, но не более 30% его значения;
- на необрабатываемых поверхностях отливки, не сопрягаемых по контуру с другими деталями, за счет увеличения «с плюсом» и уменьшения размеров отливки «с минусом» (рис. 1.18 б);
- на необрабатываемых поверхностях отливки, сопрягаемых по контуру с другими деталями, за счет уменьшения «с минусом» (рис. 1.18 в) или увеличения «с плюсом» (рис. 1.18 г) размеров отливки в зависимости от поверхностей сопряжения.
г |
в |
б |
а |

Рисунок 1.18. Формовочные уклоны: Н, h – высота модели
Для необрабатываемых поверхностей обычно применяются уклоны, приведенные в табл. 1.6.
Таблица 1.6.
Уклоны для необрабатываемых поверхностей отливок
Толщина стенок, мм | До 8 | 8–12 | Свыше 12 |
Уклон | «с плюсом» | «с плюсом и минусом» | «с минусом» |
Поверхности, подвергающиеся механической обработке, кроме припусков на обработку, имеют уклоны «с плюсом».
В тех случаях, когда модель образует в форме выступы и впадины или форма изготовляется из песчано-глинистых смесей, – уклон увеличивается на 50 – 100 % (β не больше 3°). Местные низкие приливы делают обычно с уклоном в 5–10°.
Величина литейных уклонов в зависимости от высоты модели Н для различных видов литья представлены в таблицах 1.7 – 1.9. (ГОСТ 3212-92).
Таблица 1.7.
Формовочные уклоны модельных комплектов для песчано-глинистых смесей
Высота Н, мм | Формовочный уклон β комплекта | |||
металлического | деревянного | |||
град. | мм | град. | мм | |
До 10 | 2°20¢ | 0,40 | 2°20¢ | 0,5 |
11…16 | 1°35¢ | 0,45 | 2°55¢ | 0,55 |
17….25 | 1°10¢ | 0,50 | 1°55¢ | 0,65 |
26…40 | 50¢ | 0,60 | 1°30¢ | 0,75 |
41…63 | 35¢ | 0,65 | 1°05¢ | 0,85 |
64…100 | 25¢ | 0,75 | 45¢ | 1,00 |
101…160 |
20¢ | 0,95 | 35¢ | 1,20 |
161…250 | 1,45 | 25¢ | 1,85 | |
251…400 | 2,30 |
20¢ | 2,30 | |
401…630 | 3,65 | 3,65 | ||
631…1000 | 5,80 | 5,80 | ||
1001…1600 | 9,30 | 9,30 | ||
1601…2500 | 14,50 | 14,50 |
Таблица 1.8
Значения формовочных уклонов формообразующих поверхностей модельных комплектов, предназначенных для форм, твердеющих в контакте с оснасткой (жидкотвердеющие самотвердеющие смеси - ЖСС, холоднотвердеющие смеси - ХТС, жидкостекольные пластичные самотвердеющие смеси - ПСС), и оболочковых форм
Высота h, мм | Формовочный уклон β комплекта | |||||
деревянного | металлического, пластмассового | для оболочковой формы | ||||
град. | мм | град. | мм | град. | мм | |
До 10 | 4°00' | 0,70 | 3°30' | 0,60 | 1°45' | 0,30 |
" 16 | 2°50' | 0,80 | 2°35' | 0,70 | 1°15' | 0,35 |
" 16 " 25 | 2°20' | 1,00 | 1°55' | 0,85 | 60' | 0,45 |
" 25 " 40 | 1°30' | 1,05 | 1°20' | 0,95 | 40' | 0,50 |
" 40 " 63 | 1°05' | 1,20 | 55' | 1,00 | 30' | 0,55 |
" 63 " 100 | 45' | 1,30 | 40' | 1,20 | 25' | 0,75 |
" 100 " 160 |
35' | 1,65 |
30' | 1,40 | 20' | 0,95 |
" 160 " 250 | 2,55 | 2,20 | 15' | 1,10 | ||
" 250 " 400 | 4,10 | 3,50 | ||||
" 400 " 630 | 6,45 |
25' | 4,60 | |||
" 630 " 1000 |
30' | 8,70 | 7,30 | |||
" 1000 " 1600 | 13,95 | |||||
" 1600 " 2500 | 21,75 |
Примечание: Значения формовочного уклона в линейных размерах даны для максимального размера h.
Значения формовочного уклона в углублениях моделей и на участках форм между моделями для ПГС и твердеющих в оснастке при d > h следует увеличивать в два раза по сравнению со значениями, указанными в табл.1.7 и 1.8.
При d < h углубления выполнять стержнем без уклонов или с уклонами по табл.1.7 и 1.8, d - диаметр, ширина углубления модели или расстояние между ними.
Таблица 1.9
Значения формовочных уклонов для литья по выплавляемым моделям
Высота модели, H мм | Формовочный уклон β | |||
для наружных поверхностей | для внутренних поверхностей | |||
град. | мм | град. | мм | |
До 10 | 30' | 0,08 | 1°30' | 0,26 |
Св. 10 " 16 | 20' | 0,09 | 1°00' | 0,28 |
" 16 " 25 | 15' | 0,10 | 45' | 0,33 |
" 25 " 40 | 0,16 | 0,52 | ||
" 40 " 63 | 10' | 0,18 | 30' | 0,55 |
" 63 " 100 | 0,29 | 0,87 |
Примечание. При изготовлении моделей в ручных пресс-формах значения формовочных уклонов могут быть увеличены в 1,5 раза.
Величина уклонов может составлять до 3° в зависимости от высоты модели. Формовочные уклоны задаются также моделям «болванов» и знаковым частям стержней (до 15°). Пример применения формовочных уклонов представлен на рисунке 1.19.
г |
в |
е |
д |
а |
б |

Рис. 1.19. Применение формовочных уклонов в отливках:
а, в, д – неправильное; б, г, е – правильное
Припуски на механическую обработку и усадку (рис. 1.20). Он зависит от материала отливки, способа литья, объёма производства, положения обрабатываемой поверхности в форме.
Рис. 1.20. Припуски на механическую обработку и усадку. 1 – формовочные уклоны, 2 – припуски механическую обработку и усадку
Припуск на усадку – слой металла, компенсирующий уменьшение объема отливки во время кристаллизации и остывания. Он зависит от величины усадки применяемого сплава.
Плоскость разъёма. Для получения внутренней полости при формовке для заливки расплава, модель делится плоскостями разъёма, чаще всего на две части. Обычно плоскость разъёма совпадает с одной из осей симметрии отливки. Этим достигается выполнение правила параллельных лучей и экономия литейных материалов за счёт меньших затрат металла на изготовление уклонов.
Для предотвращения образования при кристаллизации усадочных раковин в отливках, в форме выполняется технологический прилив, который застывает в последнюю очередь. Этот прилив называется прибылью (рис. 1.21). Прибыль устанавливается в том месте формы, где расположен наибольший объём жидкого металла.
Рис. 1.21. Расположение прибыли – 1 на отливке
Минимальные толщины стенки при различных видах литья, зависят от массы отливки, длины стенки, площади внешней поверхности отливки, габаритных размеров (N) отливки. Она назначается так, чтобы обеспечить необходимую расчетную прочность и удовлетворить требованиям технологии выбранного способа литья. Наименьшую толщину стенок определяют в зависимости от приведенного габарита заготовки:
– для прямоугольных в плане отливок:
где l, b, h – соответственно длина, ширина и высота заготовки;
- для круглых в плане отливок:
где d – диаметр отливки h – ширина.
Если приведенный габарит N окажется больше 8, толщину стенок принимают для стальных и чугунных отливок соответственно не менее 40 и 30 мм. При N не более 0,1 минимальную толщину стенок принимают: для алюминиевых сплавов – до 2 мм, для медных оловянных сплавов – 2,5, для безоловянных сплавов – 4 мм.
В зависимости от материала и его охлаждения вводят следующие корректировки:
- толщина внутренних стенок чугунных и алюминиевых отливок должна быть на 10–20 % меньше толщины наружных стенок;
- для отливок из модифицированного и высокопрочного чугунов толщину стенок увеличивают на 15–20 % по сравнению с отливками из серого чугуна;
- для отливок из легированных сталей, толщину стенки увеличивают на 20–30 % по сравнению с однотипными отливками из углеродистых сталей.
Таблица 1.10
Минимальная толщина стенки отливки при литье в песчаные формы
Материал | Масса отливки, кг | Максимальная длина стенки, мм | Минимальная толщина стенки, мм |
Сталь | До 100 | До 200 | 8…10 |
100…1000 | 200…800 | 12…14 | |
Серый чугун | До 100 | До 200 | 3…4 |
100…1000 | 200…800 | 6…8 | |
Ковкий чугун | До 100 | До 100 | 2,5…3,5 |
100…300 | 100…200 | 4…5,5 | |
Бронза оловянистая | До 10 | До 50 | 3…4 |
10…50 | 50…100 | 5…6 | |
Св.50 | Св.100 | 7…8 | |
Бронзы и латуни специальные | До 0,25 | До 50 | 6…7 |
0,25…4,0 | 50…100 | 8…10 | |
Алюминиевые сплавы | До 2,0 | До 200 | 3…5 |
2,0…10,0 | 200…500 | 6…8 | |
Магниевые сплавы | До 2 | До 200 | 3,5…4,5 |
2…8 | 200…400 | 6…7 |
Таблица 1.11
Минимальная толщина стенок отливки при литье под давлением, мм.
Материал | Площадь внешней поверхностей отливок, см2 | ||||
до 25 | 25-100 | 100-250 | 250-500 | св. 500 | |
Цинковые сплавы | 0,5 | 0,8 | 1,0 | 1,5 | 2,0 |
Алюминиевые сплавы | 0,8 | 1,2 | 1,5 | 2,5 | 3,0 |
Магниевые сплавы | 1,0 | 1,5 | 2,0 | 2,5 | - |
Медные сплавы | 2,0 | 2,5 | 3,0 | 3,5 | - |
Таблица 1.12
Минимальная толщина стенок отливки при кокильном литье, мм
Материал | Площадь поверхности стенки, см2 | Минимальная толщина стенки, мм |
Чугун | До 5 | 4…5 |
Чугун | 25…125 | 6…7 |
Сталь | 25…125 | 8 |
Алюминиевые сплавы | До 30 | 3…4 |
Магниевые сплавы | До 30 | 3 |
Бронза | До 30 | 4…6 |
Таблица 1.13
Наименьшая толщина стенок отливок при литье в оболочковую форму, мм.
Материал | Наибольший габаритный размер отливок, мм | ||||
До 100 | Св. 100 до 200 | Св. 200 до 350 | Св. 350 до 500 | Св. 500 до 1500 | |
Чугуны | 2,5…3,5 | 2,5…4,0 | 3,0…4,5 | 4,0…5,0 | 8,0…10,0 |
Стали | 2,5…4,0 | 3,0…3,5 | 3,5…6,0 | 5,0…7,0 | 8,0…12,0 |
Алюминиевые сплавы | 2,5…4,0 | 3,0…5,0 | 4,0…6,0 | 4,0…7,0 | 7,0…10,0 |
Магниевые сплавы | 2,5…4,0 | 3,0…4,0 | 3,5…5,0 | 4,0…6,0 | 7,0…10,0 |
Цинковые сплавы | 2,0…4,0 | 2,5…3,5 | 3,0…4,0 | 3,5…5,0 | 7,0…10,0 |
Медные сплавы | 2,5…4,0 | 3,0…4,0 | 3,0…5,0 | 4,0…6,0 | 5,0…7,0 |
Бронзы оловянистые | 1,5…2,0 | 2,0…3,0 | 2,5…3,5 | 3,0…4,0 | 4,0…6,0 |
Для отливок, получаемых литьем в песчано-глинистые формы, минимальную толщину стенок также можно определить по графикам (рис. 1.22.).
а |

б |

в |
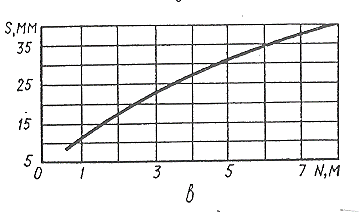
Рис. 1.22. Графики для определения толщины стенок S отливок от габаритного размера N, полученных в песчаных формах:
а – из углеродистых сталей (1) и чугуна (2); б – из медных безоловянных (1) и оловянных (2) сплавов; в – из алюминиевых сплавов